Membrane Switch Manufacturer Offering High-Accuracy Engineering Solutions
Exploring the Production Process of Membrane Switch for Numerous Industries
The production procedure of Membrane buttons is an intricate venture that requires accuracy and attention to detail. From choosing appropriate materials to applying strenuous quality assurance steps, each step plays an important role in guaranteeing capability. Different industries, consisting of auto and medical, depend on these components for their special applications. Comprehending the intricacies of this process reveals substantial understandings into how these buttons are produced and their impact throughout diverse markets.
Comprehending Membrane Switches: An Overview
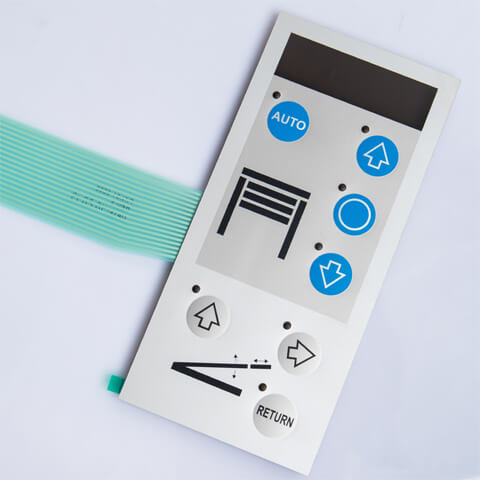
Key Materials Made Use Of in Membrane Switch Manufacturing
In Membrane button production, the selection of essential products significantly influences capability and durability. Conductive products, adhesives, and finishings play important duties, while substrate selection impacts total performance and integrity. Comprehending these elements is crucial for enhancing the design and manufacturing of Membrane buttons.
Conductive Products Overview
Conductive materials play an important function in the capability of Membrane buttons, guaranteeing reliable electrical connections within the device. Commonly made use of materials consist of silver, copper, and carbon-based inks, each offering unique benefits. Silver is favored for its high conductivity and toughness, making it optimal for applications requiring durable efficiency. Copper, while somewhat much less conductive than silver, is an economical choice frequently made use of in printed circuits. Carbon-based inks give a versatile alternative, appropriate for applications where flexibility and lower costs are prioritized, although they have actually reduced conductivity contrasted to steel options. The selection of conductive materials straight influences the total integrity, lifespan, and efficiency of the Membrane button, making it a vital factor to consider in the manufacturing process.
Adhesives and Coatings
Coverings and adhesives are crucial components in the manufacturing of Membrane buttons, giving essential bonding and protective properties. These materials ensure that different layers of the button, including graphic overlays and wiring, stick firmly to one an additional, improving durability and functionality. Typically used adhesives consist of pressure-sensitive adhesives (PSAs) and epoxy-based formulations, which use solid adhesion and strength. Coatings, such as polyurethane or acrylic, serve to shield against environmental elements, including dampness, abrasion, and chemicals. Furthermore, layers can boost responsive feedback and aesthetic charm, contributing to the total individual experience. The selection of proper adhesives and coverings is crucial for optimizing efficiency and longevity in diverse applications throughout different industries, guaranteeing that Membrane switches fulfill particular functional demands.
Substratum Option Elements
Substratum selection plays a necessary duty in the manufacturing of Membrane switches, as it substantially affects their overall efficiency and resilience. Trick products such as polyester, polycarbonate, and versatile published circuit card (FPCBs) are generally utilized for their distinct residential properties. Polyester is favored for its cost-effectiveness and resistance to abrasion, making it appropriate for applications with high wear. Polycarbonate deals exceptional quality and impact resistance, suitable for settings calling for high exposure. FPCBs give enhanced versatility and are commonly utilized in intricate designs. The choice of substratum additionally impacts variables like thermal stability, chemical resistance, and ease of printing. Eventually, picking the appropriate substrate is crucial for ensuring the capability and longevity of Membrane switches throughout numerous markets.
The Layout Refine of Membrane Changes
The layout procedure of Membrane switches is a critical stage that substantially influences the functionality and aesthetic appeals of the end product - membrane switch manufacturer. It begins with defining the particular needs of the application, consisting of dimensions, switch layout, and tactile responses choices. Developers need to consider individual communication, making sure that the switch is intuitive and accessible.Next, materials are selected based on durability, adaptability, and ecological resistance. The combination of graphics and branding aspects is also important, as it enhances visual charm and interaction. Prototyping enables for repetitive testing, allowing changes based upon individual feedback and efficiency evaluations.Additionally, the design should represent the electrical elements, such as circuits and connectors, making certain integrity and convenience of use. Eventually, an effective design harmonizes performance, looks, and individual experience, paving the way for efficient production and long-lasting efficiency in various markets
Printing Techniques for Membrane Switches
The printing strategies made use of in Membrane switch manufacturing play a crucial role in determining the last item's high quality and capability. Display printing provides advantages such as toughness and vivid color application, while digital printing innovations provide flexibility and precision in style. Understanding these methods can substantially impact the total performance of Membrane buttons in numerous applications.
Screen Printing Advantages
Countless advantages make display printing a recommended strategy for producing Membrane switches. This technique enables premium, thorough layouts and vibrant colors, which are vital for interface applications. Display printing is specifically efficient for using thick ink layers, improving longevity and responsive responses. Additionally, it offers outstanding adhesion to different substratums, making sure longevity sought after atmospheres. The process is cost-effective for huge manufacturing runs, as it lessens arrangement time and waste. Display printing supports a broad range of inks, consisting of specialized and UV-curable choices, enabling flexibility in layout. Its capacity to produce regular outcomes across numerous devices makes it a trusted selection for makers going for quality and performance in Membrane switch manufacturing.
Digital Printing Innovations
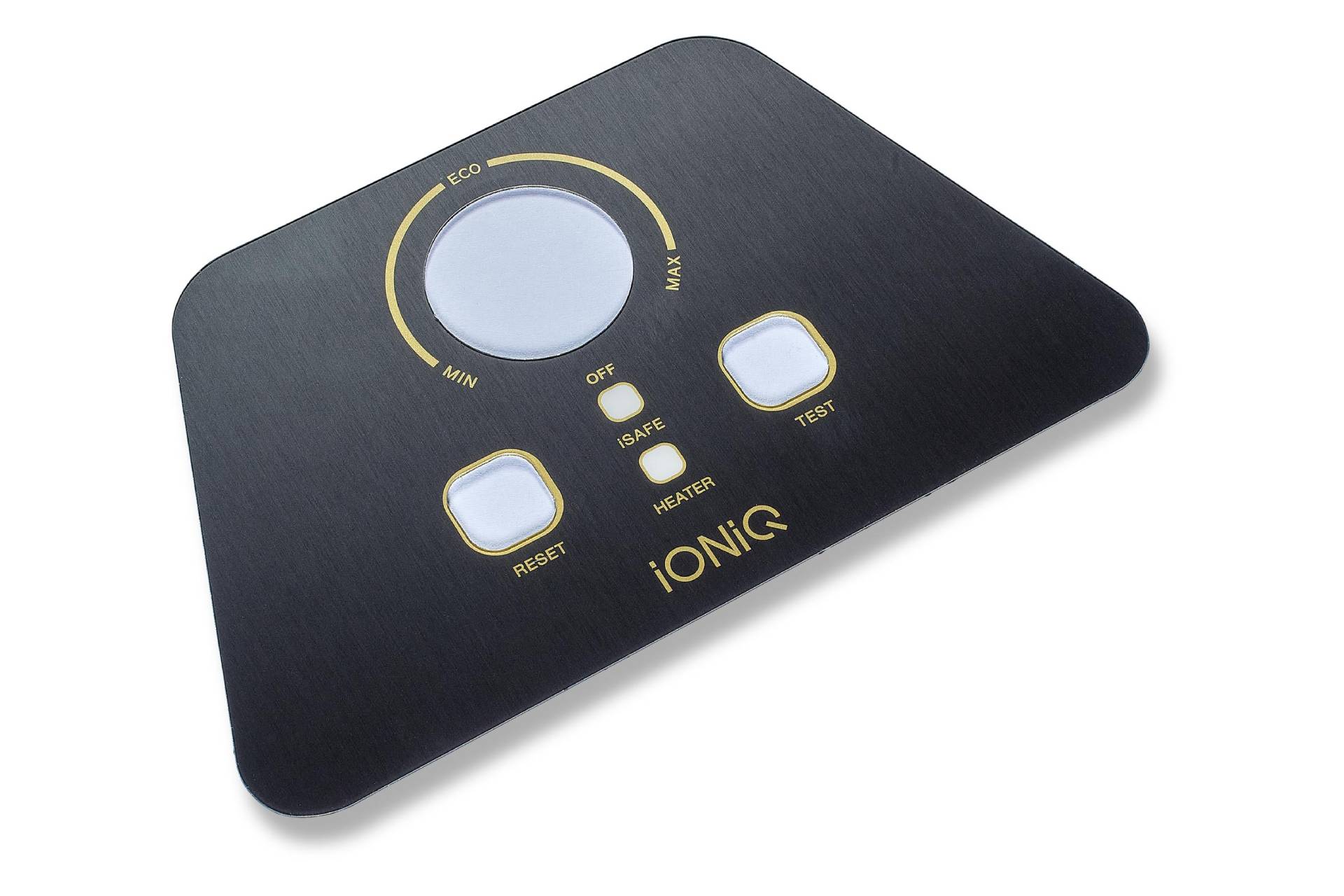
Developments in digital printing innovation are changing the production of Membrane buttons, offering suppliers ingenious services that enhance layout versatility and effectiveness. Digital printing permits complex layouts and high-resolution graphics, allowing personalized branding and performance without the constraints of conventional techniques. This technique decreases setup times and costs, facilitating shorter production runs and minimal waste, making it excellent for organizations with varying demands. Furthermore, innovations in ink formulas give much better toughness and adhesion, guaranteeing long life in various environments. As industries increasingly seek tailored and intricate layouts, electronic printing attracts attention as a vital technique, establishing a brand-new standard in Membrane switch production. The integration of these advancements settings producers to satisfy progressing market needs efficiently.
Assembly and Layering of Membrane Switch Elements
Cautious assembly and layering of Membrane button elements are necessary to guaranteeing performance and durability. This process begins with the precise placement of numerous layers, including the visuals overlay, sticky, circuit layer, and backing product. Each component has to be thoroughly placed to maintain electric honesty and interface responsiveness.During setting up, conductive traces are related to the circuit layer, usually made from products like polyester or polycarbonate. This layer is important, as it transmits signals when stress is used. The sticky made use of for bonding these layers is also picked for its ability to sustain ecological anxieties while preserving a protected bond.Heat and stress are typically used during the assembly procedure to establish that the layers adhere appropriately without jeopardizing the performance of the switch. Finally, focus is offered to the edge securing to shield against wetness and impurities, securing the longevity of the Membrane button in different industrial applications.
Quality Assurance Steps in Membrane Switch Manufacturing
Quality assurance actions play a vital function in making sure the reliability and performance of Membrane switches adhering to the assembly and layering of their elements. In the production process, numerous key examinations are conducted to copyright top quality standards. These consist of aesthetic evaluations for flaws in printing and sticky application, along with functional tests to confirm the responsiveness of each switch.Additionally, environmental screening is executed to assess the switches' toughness against temperature level fluctuations and humidity Home Page direct exposure. Makers commonly implement statistical process control (copyright) methods to monitor production consistency, making it possible for very early detection of anomalies.Furthermore, traceability systems are developed to track products and components, ensuring liability and assisting in recalls if required. Calibration of equipment and adherence to sector criteria are also vital to maintaining product integrity. Jointly, these quality control measures protect the efficiency of Membrane switches over throughout different applications, ultimately enhancing customer fulfillment.
Applications of Membrane Changes Across Different Industries
Membrane switches are utilized throughout a varied selection of industries, showcasing their versatility and flexibility. In the clinical market, they supply waterproof and reliable user interfaces for tools such as analysis equipment and mixture pumps, ensuring hygiene and ease of use. The automotive industry employs Membrane switches for dashboard controls, enabling smooth interaction in between the chauffeur and lorry systems.In customer electronics, these switches are discovered in appliances and handheld tools, offering a sleek, modern aesthetic while improving capability. Industrial applications also utilize Membrane changes for machinery control panels, where longevity and resistance to extreme conditions are essential.Furthermore, the aerospace and protection fields make use of Membrane buttons for cockpit instrumentation and interaction systems, focusing on dependability and efficiency under extreme conditions. Generally, Membrane switches play an important role in boosting the user experience and functional efficiency throughout various domain names.
Regularly Asked Questions
The length of time Does It Take to Produce a Membrane Layer Switch?
The production time for a membrane switch commonly ranges from a few days to numerous weeks - membrane switch manufacturer. Factors affecting this period consist of design complexity, product availability, and manufacturing volume, all affecting the general timeline noticeably
What Is the Common Lifespan of a Membrane Switch?
The normal life-span of a membrane layer button typically varies from 1 to 5 million actuations, depending here are the findings on factors such as material quality, environmental problems, and usage frequency, considerably affecting longevity and overall performance.
Can Membrane Switches Be Personalized for Details Applications?
Membrane switches can without a doubt be customized for details applications. Their layout flexibility our website allows for alterations in size, form, shades, and graphics, making certain compatibility with one-of-a-kind needs across various industries and improving functionality and user experience.
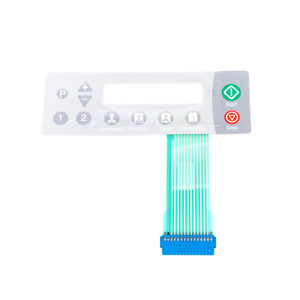
Are Membrane Switches Eco-friendly?
The ecological impact of Membrane switches over varies. Some products utilized might not be environmentally friendly, while innovations in manufacturing procedures are progressively concentrating on sustainability, aiming to minimize waste and advertise recyclable elements in their manufacturing.
What Are the Common Failure Settings of Membrane Buttons?
Usual failure modes of Membrane buttons include delamination, sticky failing, deterioration from use, wetness ingress, and electric failings. These problems can greatly affect performance, efficiency, and lifespan in various applications throughout different industries. Membrane switches can be customized to fit certain design needs, such as shape, dimension, and capability, making them extremely adaptable.The building commonly entails several layers, including a visuals overlay, adhesive, and a circuit layer, which work together to produce a seamless individual experience. In Membrane switch manufacturing, the choice of vital products considerably influences performance and resilience. The automobile industry employs Membrane buttons for control panel controls, making it possible for smooth communication between the motorist and automobile systems.In customer electronics, these buttons are found in devices and portable gadgets, providing a sleek, contemporary aesthetic while enhancing functionality. Industrial applications also take advantage of Membrane switches for equipment control panels, where durability and resistance to rough problems are essential.Furthermore, the aerospace and protection fields use Membrane buttons for cockpit instrumentation and interaction systems, prioritizing dependability and performance under severe conditions. Membrane switches can undoubtedly be customized for specific applications.